Mechanical:
Mounted the pivot plates, removed silicon, replaced steel shafts, and shooter plates are being recut of CNC. We had to change the placement of the battery so it was not rested and laid down horizontally since the cable routing wouldn’t work that way. Because of this, we had to move the shaft plates up to make the battery vertical.
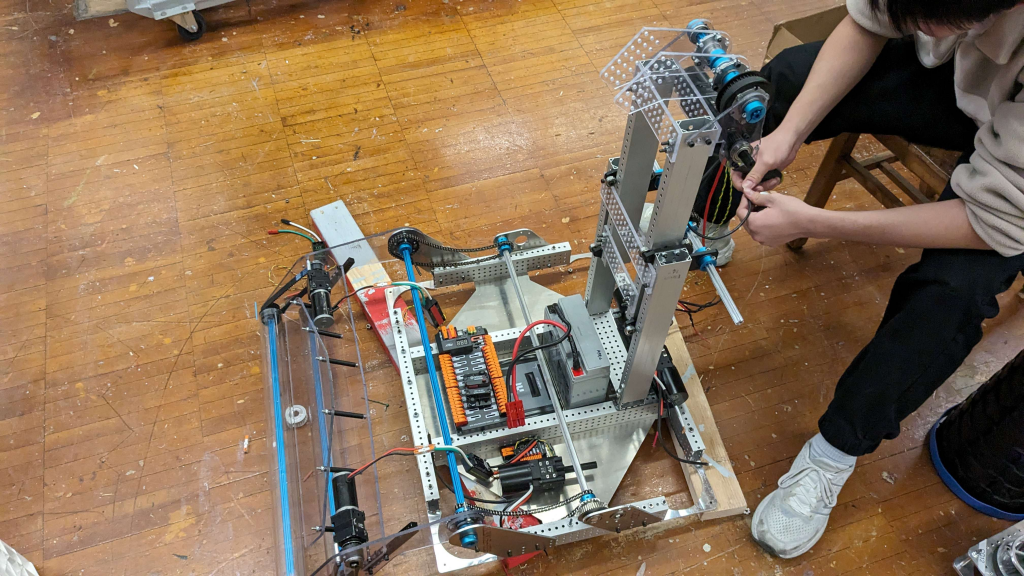
Intake:
Mounted the second motor on the intake and used an 80-tooth belt for both of the intake pieces. Using our 3D printer, we printed standoffs for the note holder. Mounted the spacers and the holder mechanism using 3D printed Nut strips and 5/16th head bolts (10-32s for WCP nutstrips). There was an issue with the deadaxle spinning the shaft so it could not spin properly. The issue was fixed by removing the deadaxle and re-installing it. We used smaller 10-32 bolts to attach the side intake plates to the chassis and mounted it to the chassis of the robot as well as sanded down the spacers. We had to move the mounting of the intake for spacing on the chassis. Silicon makes the intake faster but makes the ring unmovable so we need to remove it. Replaced the churros within the rollers in order to stabilize them.
Gearbox Motor Math:
We need to compute the required gearing on the intake pivot mechanism (this will raise and lower the whole intake allowing us to pull it inside frame perimeter).
Weight: 8lbs Center Of Mass (COM): 7″ away from the pivot point
We might add more structure to the intake. Over-estimate is 15lbs ⇒ 6.81 Kg
T = 7*2.54/100 * 6.81 = 1.21 Nm
This is very little required torque. But we still need to slow this down and running at very low power will reduce the wattage too much. The current design involves a 48:1 gear ratio.
The middle of the motor curve is 3000 rpm, so we have 3000 / 48 = 62.5 rpm = 1.04 rotations per second.
Elevator:
Finished the widened elevator with the correct length and mounted the motors to the baseplate of the elevator. The baseplate’s holes were not aligned so we had to CNC another baseplate in order for everything to line up. We then mounted the elevator on the chassis with 1/4 20’s. We needed to use the angle grinder to shorten the length of it since it was interfering with a bolt on the elevator.
KOP Bot:
The programming for the kit of parts bot has been completed in order for practice driving and operating it. We need to order 72″ Orange Reflective Rod (fiberglass rod) for the amp scorer component of the everybot since we are trying to make the KOP bot into the Robonauts 2024 Everybot. We are using the climber for the 2022 season on the robot and have begun to work on each component.