We decided to not test our week 3 shooting mechanism with a motor because it looked like we couldn’t get the wheel to make enough contact with the ball. We debated how and where to add another wheel for further acceleration and the team decided to build a dual wheel system similar to what we used for a ball intake in 2019.
A little torque literally goes a long way
In order to maximize the motor speed, students first built the shooting mechanism with a 1:1 gear box using two 775 motors. These motors have a surprisingly high RPM of over 9000 for peak power. But the torque at peak power is only 0.3 Newton Meters or 2.66 inch pounds. This is so low that the shooter was unable to give the ball much momentum.
We swapped out the gear boxes and used a 5:1 ratio. This can still give us a wheel speed around 2000 RPM, but with five times the torque. The ball hit the 11 foot ceiling. The prototype was a success!
The ball track prototype was designed last week, but we didn’t get a chance to see how a ball would move through it until this week.
The last thing we want to see at competition is a power cell stuck inside our machine, unable to move to the shooter. It looked like this could happen with the design shown here.
Our mechanical lead first suggested adding belts to help it move along. After some experimentation and contemplation, he got to work a redesign. Blake, out team captain from last year, joined us as a mentor on Saturday and helped students think through this system.
We decided to redesign this track with the goal of always having two wheels in contact with each ball. We also decided that we want to launch the ball at 40°.
Can we get it working?
Yes, we CAD!
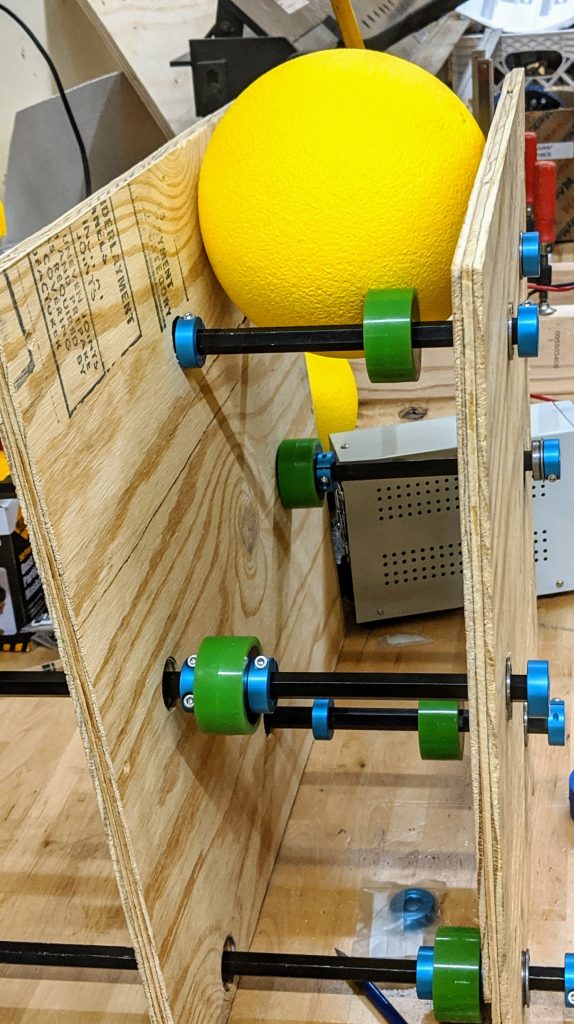